One of the most important accessories for any temperature-sensing element is a pressure-tight sheath known as a thermowell. This may be thought of as a thermally conductive protrusion into a process vessel or pipe27 allowing a temperature-sensitive instrument to detect process temperature without opening a hole in the vessel or pipe. Thermowells are critically important for installations where the temperature element (RTD, thermocouple, thermometer, etc.) must be replaceable without de-pressurizing the process.
Thermowells may be made out of any material that is thermally conductive, pressure-tight, and not chemically reactive with the process. Most thermowells are formed out of either metal (stainless steel or other alloy) or ceramic materials. A simple diagram showing a thermowell in use with a temperature gauge is shown here:
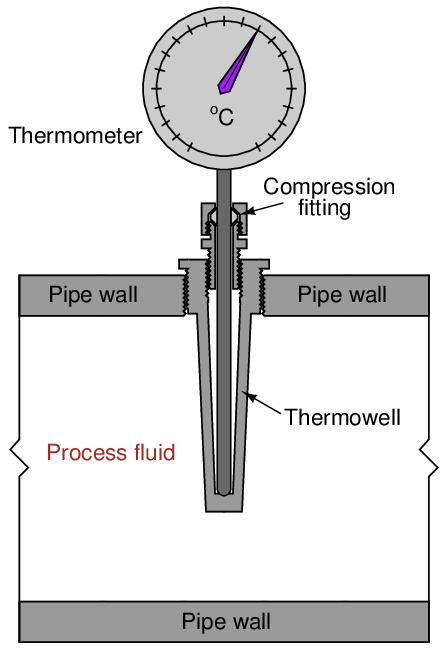
If the temperature gauge is removed for maintenance or replacement, the thermowell maintains pressure integrity of the pipe (no process fluid leaking out, and no air leaking in):
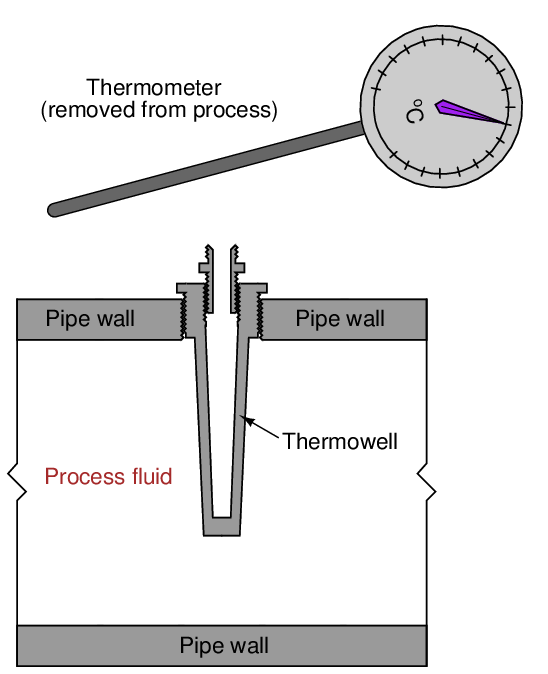
Photographs of a real (stainless steel) thermowell are shown here, the left-hand photo showing the entire length of the thermowell, and the right-hand photo showing the end where the temperature-sensing device is inserted:
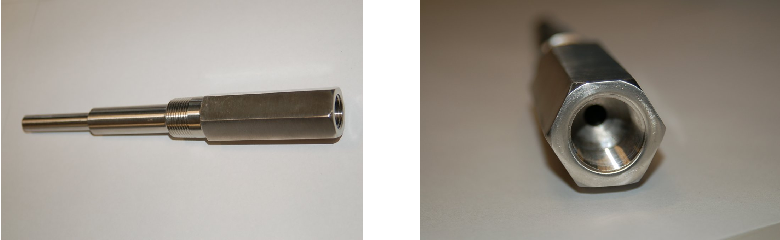
A photo of a complete RTD assembly (connection head, RTD, and thermowell) appears in the next photograph:
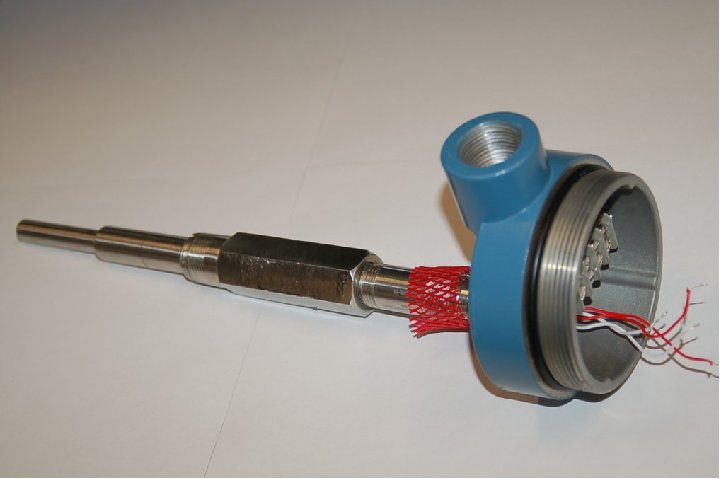
Another photo shows an RTD installed in a thermowell on the side of a commercial freezer, using a Rosemount model 3044C temperature transmitter to output a 4-20 mA signal to an operator display:
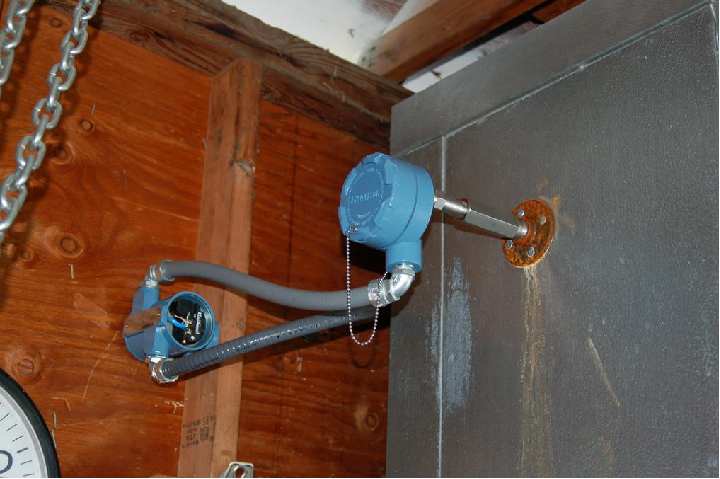
As useful as thermowells are, they are not without their caveats. All thermowells, no matter how well they may be installed, increase the first-order time lag of the temperature sensor by virtue of their mass and specific heat value. It should be intuitively obvious that a few pounds of metal will not heat up and cool down as fast as a few ounces’ worth of RTD or thermocouple, and therefore the addition of a thermowell to the sensing element will decrease the responsiveness of any temperature-sensing element. What is not so obvious is that such time lags, if severe enough, may compromise the stability of feedback control. A control system receiving a “delayed” temperature measurement will not see the live temperature of the process in real time due to this lag.
A potential problem with thermowells is incorrect installation of the temperature-sensing element. The element must be inserted with full contact at the bottom of the thermowell’s blind hole. If any air gap is allowed to exist between the end of the temperature element and the bottom of the thermowell’s hole, this will add a second time lag to the measurement system28 . Some thermowells include a spring clip in the bottom of the blind hole to help maintain constant metal-to-metal contact between the sensing element and the thermowell wall.
21.7 Process/instrument suitability
The primary consideration for selecting a proper temperature sensing element for any application is the expected temperature range. Mechanical (bi-metal) and filled-system temperature sensors are limited to relatively low process temperatures, and cannot relay signals very far from the point of measurement.
Thermocouples are by far the most rugged and wide-ranging of the contact-type temperature sensors. Accuracies vary with thermocouple type and installation quality.
RTDs are more fragile than thermocouples, but they require no reference compensation and are inherently more linear.
Optical sensors lack the ability to measure temperature of fluids inside vessels unless a transparent window is provided in the vessel for light emissions to reach the sensor. Otherwise, the best an optical sensor can do is report the skin temperature of a vessel. For monitoring surface temperatures of solid objects, especially objects that would be impractical or even dangerous to contact (e.g. electrical insulators on high-voltage power lines), optical sensors are the only appropriate solution.
Chemical reactivity is a concern for contact-type sensors. If the sensing element is held inside a thermowell, that thermowell must be selected for minimum reaction with the process fluid(s). Bare thermocouples are particularly vulnerable to chemical reactions given the nature of most thermocouple metals (iron, nickel, copper, etc.), and must be carefully chosen for the particular process chemistry to avoid reliability problems later.
21.8 Review of fundamental principles
Shown here is a partial listing of principles applied in the subject matter of this chapter, given for the purpose of expanding the reader’s view of this chapter’s concepts and of their general inter-relationships with concepts elsewhere in the book. Your abilities as a problem-solver and as a life-long learner will be greatly enhanced by mastering the applications of these principles to a wide variety of topics, the more varied the better.
- Kirchhoff’s Voltage Law: the algebraic sum of all voltages in a loop is equal to zero. Relevant to thermocouple circuit calculations, where the reference junction voltage always opposes the measurement junction voltage. Also relevant to RTD circuits when determining the amount of voltage sensed by the instrument compared to the amount of voltage dropped by the RTD resistance element.
- Ideal Gas Law: PV = nRT, describing the relationship between gas pressure, chamber volume, gas quantity (in moles), and gas temperature. Relevant to Class III filled-bulb temperature sensors, where the increased pressure of an enclosed gas corresponds to the temperature of that gas.
- Self-balancing opamp circuits: all self-balancing operational amplifier circuits work on the principle of negative feedback maintaining a nearly zero differential input voltage to the opamp. Making the “simplifying assumption” that the opamp’s differential input voltage is exactly zero assists in circuit analysis, as does the assumption that the input terminals draw negligible current.
- Stefan-Boltzmann Law: dQ dt = eσAT4, that all objects warmer than absolute zero radiate thermal energy (photons). Relevant to non-contact pyrometry, where the intensity of the received radiation is proportional to the fourth power of the object’s absolute temperature.
- Time constant: (τ), defined as the amount of time it takes a system to change 63.2% of the way from where it began to where it will eventually stabilize. The system will be within 1% of its final value after 5 time constants’ worth of time has passed (5τ). Relevant to temperature lags caused by sensor mass and thermowells.
- Inverse square law: the strength of a field radiating away from a point-source diminishes proportionately to the square of the distance from the source. Relevant to determining the amount of radiant energy intercepted by a sensor when monitoring a point-source of heat.
References
Baker, Bonnie C., “Precision Temperature-Sensing With RTD Circuits”, application note AN687, Microchip Technology Incorporated, 2003.
Beckerath, Alexander von; Eberlein, Anselm; Julien, Hermann; Kersten, Peter; and Kreutzer, Jochem, WIKA-Handbook, Pressure and Temperature Measurement, WIKA Alexander Wiegand GmbH & Co., Klingenberg, Germany, 1995.
Darling, Charles Robert, Pyrometry – A Practical Treatise on the Measurement of High Temperatures, E. & F.N. Spon, Ltd, London, 1911.
Fribance, Austin E., Industrial Instrumentation Fundamentals, McGraw-Hill Book Company, New York, NY, 1962.
Irwin, J. David, The Industrial Electronics Handbook, CRC Press, Boca Raton, FL, 1997.
Kallen, Howard P., Handbook of Instrumentation and Controls, McGraw-Hill Book Company, Inc., New York, NY, 1961.
Lipták, Béla G. et al., Instrument Engineers’ Handbook – Process Measurement and Analysis Volume I, Fourth Edition, CRC Press, New York, NY, 2003.
“Model 444 Alphaline Temperature Transmitters”, Document 00809-0100-4263, Revision AA, Rosemount, Inc., 1998
“Radiamatic Detectors and Accessories”, Specification document 23-75-03-03, Honeywell, Inc., Fort Washington, PA, 1992.
“Temperature – Electromotive Force (EMF) Tables for Standardized Thermocouples”, Pyromation, Inc.
“Temperature Measurement – Thermocouples”, ISA-MC96.1-1982, Instrument Society of America, Research Triangle Park, NC, 1982.