The following photograph shows a large air blower in a wastewater treatment facility equipped with a Bently-Nevada model 3300 vibration monitoring rack (located left-center on the foreground panel):
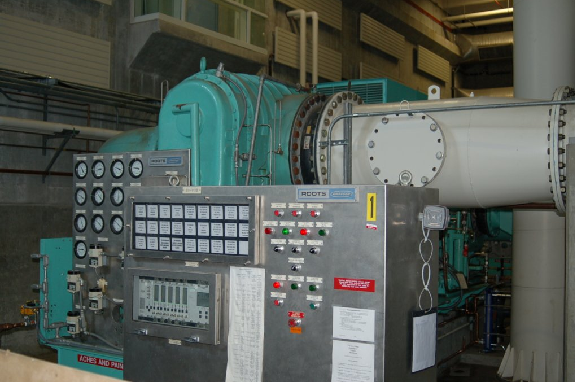
Five vibration measurement and display cards are installed in this rack, each card capable of processing up to two displacement sensor signals. A six-channel temperature monitor card is also installed in the rack, used to display bearing and other machine component temperatures. Like the vibration cards, the temperature card is capable of generating both “alert” and “trip” signals, monitoring the presence of slightly abnormal conditions and taking automatic shut-down action in the event of excessively abnormal conditions, respectively.
A closer view of a different Bently-Nevada model 3300 vibration monitoring rack is shown in this photograph:
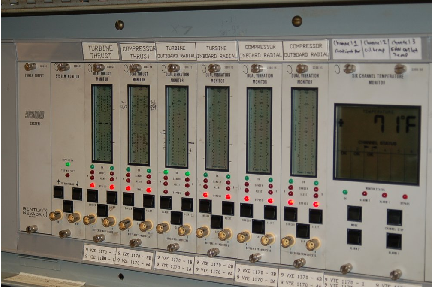
Each “card” inserted into this rack performs a different measurement function.
The following photographs show even closer views of the cards, revealing the display bargraphs and the units of measurement. From left to right; thrust measurement, vibration measurement, temperature measurement (6 channels), and speed measurement:
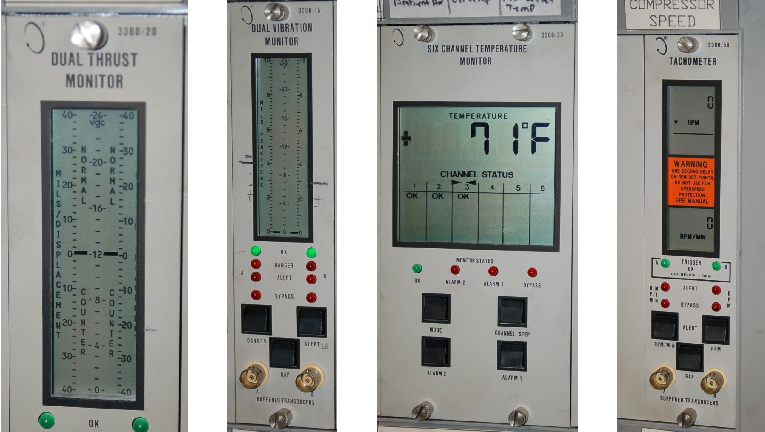
BNC-style cable connectors on the front of the cards provide convenient connection points for electronic test equipment such as oscilloscopes or spectrum analyzers. This eliminates the need to un-do wire connections on the proximitor units in order to take diagnostic measurements. Each card also provides “alert” and “danger” levels for their respective measurements, generating a contact-closure signal which may be connected to an automatic shutdown (“trip”) system to take protective action if vibration or thrust displacement ever exceeds pre-set limits.
Another variety of vibration monitoring hardware is the Bently-Nevada 1701 FieldMonitor. This hardware lacks the convenient front-panel displays of the model 3300, opting instead to communicate vibration data in digital form to an Allen-Bradley programmable logic controller (PLC). Not only does this make it possibly to display the vibration data remotely through HMI (Human-Machine Interface) panels, but it also enables vibration data to engage automatic “trip” logic programming in the PLC to shut the machine down in the event of excessive vibration. This next photograph shows several FieldMonitor modules plugged into a rack, acquiring displacement data from eight proximity probes (X and Y axis radial measurements at three machine bearing locations, plus one axial (thrust) measurement and one phase reference measurement):
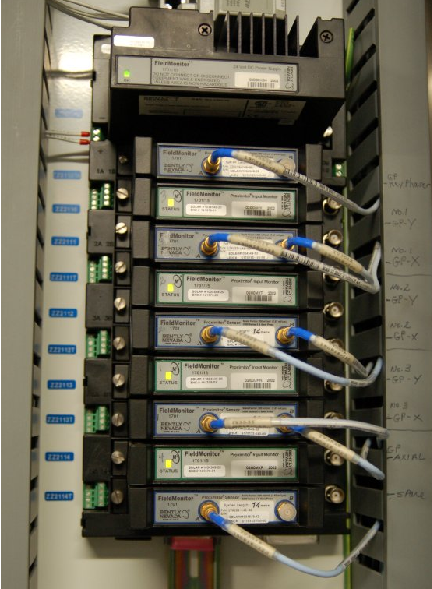