1) What is Custom Metal Fabrication?
Metal Fabrication is an important branch of mechanical engineering, which also includes custom metal fabrication that we often come into contact with. The so-called custom metal fabrication is to make the workpiece get the desired geometry, dimensional accuracy and surface quality, and to meet the hardness requirements etc… It requires a series of machining processes such as cutting, pressure forming, heat treatment, cleaning and rust prevention. Through this process metal can change its size, shape or certain characteristics so that it can be used in other applications. It can be processed by hand or machine, the choice of metal fabrication depends on its future use. Want to know more about metal machining services, especially for CNC machining aluminum, you can learn more aluminum machining tips here.
From tooling perspective, metal fabrication can be divided into: using predefined tool geometry, which includes turning, milling, sawing, drilling; metal processing without a predefined cutting edge, mainly grinding; using free blades for metal processing, including grinding , Polishing, honing; no blade treatment, including ultrasonic processing, plasma processing, laser processing, water jet processing.
From material perspective, Metal fabrication can be divided into: processing non-shaped materials, such as scrap processing; metal processing does not remove materials, such as casting; processing by removing materials, such as turning; metal processing through connecting, such as welding; metal protection, such as coloring ; Metal processing by changing properties, such as hardening; the last point is hot metal processing. Hot metal processing means that the influence of heat on the metal will change the performance of the metal and thus affect the microstructure. The most common metal for heat treatment is steel. The main reason for the treatment is increase strength first, then increase toughness and replasticity. The choice of metal processing technology depends to a large extent on the future use of the processed metal, namely accuracy and processing quality
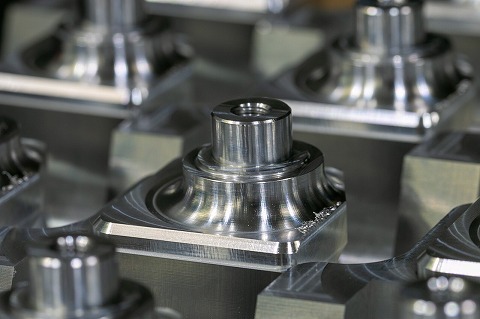
2. Benefits of Custom CNC Machining
Speaking of the benefits of customized CNC machining. The market economy is almost everywhere reflecting the theory of superiority, as is the case in the CNC machining industry. Some precision maching peers, their own factories can produce parts, but they still tend to outsource because they value the comparative advantages of partners. Mutual assistance and cooperation in the field of CNC machining is to advocate that a CNC machining factory be firmly nailed to a certain field in the entire precision machining supply chain and let it play its role.
In the traditional manufacturing industry, the market also allocates resources invisibly, cooperates to create value, and jointly promotes industrial prosperity. For example, large-scale CNC processing and customization companies can produce all products in the entire industrial chain, but they also tend to outsource some non-core products to other partners. That is to focus on their comparative advantages and continue to improve themselves in the CNC processing and customization market. And these outsourcing partners of precision mechanical parts processing, because these orders allow them to focus on this particular field, also formed their own comparative advantages in the market. This is the power of the market!
Custom design becomes easier and cheaper. The CNC machine tool can understand the CAD language and can easily convert the design into coordinates and numbers for monitoring the movement of the machine. Once the design is generated in CAD, it can be easily converted into a 3D model.
a. Flexible Multi-Axis CNC Machining
1) Multi-face processing can be completed under the condition of one clamping, so it can improve accuracy and processing efficiency;
2) Since the tool axis of the multi-axis machine tool can be changed, the attitude angle of the tool or workpiece can be adjusted at any time, so more complicated parts can be processed;
3) Because the position angle of the tool or workpiece is adjustable, it can avoid tool interference, undercutting and overcutting. Thereby obtaining a higher cutting speed and cutting line width, so that the cutting efficiency and the quality of the processed surface can be improved;
4) The application of multi-axis machine tools can simplify the shape of the tool, thereby reducing the cost of the tool. At the same time, the length-diameter ratio of the tool can be improved, so that the rigidity, cutting speed and feed speed of the tool can be greatly improved.
b. CNC Metal Lathe Machining
1) The number of tooling is greatly reduced, and complex tooling is not required to process parts with complex shapes. If you want to change the shape and size of the part, you only need to modify the part processing program, which is suitable for the development and modification of new products;
2) The production efficiency is higher in the case of multiple varieties and small batch production, which can reduce the time for production preparation, machine tool adjustment and process inspection, and reduce the cutting time due to the use of the optimal cutting amount;
3) Machining of complex surfaces that are difficult to process with conventional methods, even machining of parts that cannot be observed.
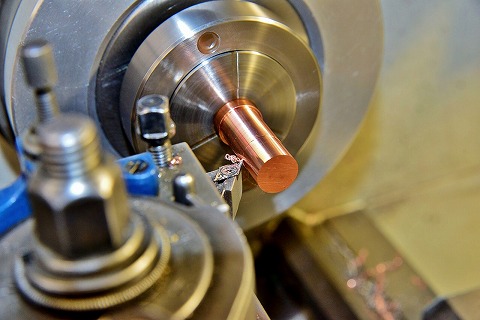
C. Wire EDM Machining
1) It can produce odd-shaped irregular surfaces that traditional cutting machines cannot produce;
2) Processing hard materials can also have good tolerance accuracy;
3)The cutting force of the traditional processing machine may damage small workpieces, but this is not the case in EDM machining;
4) The processing process is almost not affected by heat, so it can reduce the thermal shock layer and high-quality workpieces;
5) The hardness of the tools used in EDM processing does not need to be harder than the material, so it is easier to processing.
6) It can cut a narrow slit of about 0.05 mm, the wire EDM efficiency is generally 20-60 mm 2 / min, the maximum is 300 mm 2 / min, the machining accuracy is generally (+ 0.01-0.02 mm), the maximum is ( +0.004 mm). The surface roughness is generally R2.5-1.25 microns, the maximum is Ralpha 0.63 microns, and the cutting thickness is average. 40-60 mm, up to 600 mm thick
3. Manufacturing Custom Metal Parts at Wayken
Wayken mainly undertakes custom metal processing, like Aluminum machining, stainless steel machining and other metals. Our business include multiple processing like milling, lathing precision hardware, mechanical parts, hardware accessories, stainless steel shafts, various custom parts. According to different requirements of customers, we can machining different custom parts to satisfy customers.
4. Conclusion
Wayken is a professional manufacturer of custom metal parts. We are good at machining Aluminum parts, internal and external thread processing, and lathe processing. The parts we machined are widely used in various fields such as household appliances, instruments, communications, aerospace, computers, mechanical equipment, auto parts, etc. Our quality is in a superior position among domestic counterparts. We have advanced machines and strict management, established a complete set of product quality control system. Our integrity, strength and product has been recognized by the worldwide customers. Welcome your any inquiry of custom parts.